Introduction
Curing is the process of maintaining satisfactory moisture content and temperature in the concrete for a definite period of time. Hydration of cement is a long-term process and requires water and proper temperature. Therefore, curing allows continued hydration and, consequently, continued gains in concrete strength. In fact, once curing stops, the concrete dries out, and the strength gain stops; as indicated in the Figure below. If the concrete is not cured and is allowed to dry in air, it will gain only about 50% of the strength of continuously cured concrete. If concrete is cured for only three days, it will reach about 60% of the strength of continuously cured concrete; if it is cured for seven days, it will reach 80% of the strength of continuously cured concrete. If curing stops for some time and then resumes again, the strength gain will also stop and reactivate.
Curing has a strong influence on the properties of hardened concrete; proper curing will increase durability, strength, water tightness, abrasion resistance, volume stability, and resistance to freezing and thawing and deicers. Exposed slab surfaces are especially sensitive to curing as strength development and freeze-thaw resistance of the top surface of a slab can be reduced significantly when curing is defective.
When portland cement is mixed with water, a chemical reaction called hydration takes place. The extent to which this reaction is completed influences the strength and durability of the concrete. Freshly mixed concrete normally contain more water than is required for hydration of the cement; however, excessive loss of water by evaporation can delay or prevent adequate hydration. The surface is particularly susceptible to insufficient hydration because it dries first. If temperatures are favorable, hydration is relatively rapid the first few days after concrete is placed; however, it is important for water to be retained in the concrete during this period, that is, for evaporation to be prevented or substantially reduced. With proper curing, concrete becomes stronger, mom impermeable, and more resistant to stress, abrasion, and freezing and thawing. The improvement is rapid at early ages but continues more slowly thereafter for an indefinite period as shown in the figure.
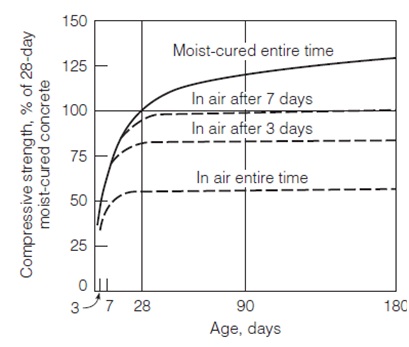
Curing should start after the final set of the cement. If concrete is not cured after setting, concrete will shrink, causing cracks. Loss of water will cause the concrete to shrink, thus creating tensile stresses within the concrete. If these stresses develop before the concrete has attained adequate tensile strength, surface cracking can result. All exposed surfaces, including exposed edges and joints, must be protected against moisture evaporation. Hydration proceeds at a much slower rate when the concrete temperature is low. Temperatures below 10°C (50°F) are unfavorable for the development of early strength; below 4°C (40°F) the development of early strength is greatly retarded; and at or below freezing temperatures, down to -10°C (14’F), little or no strength develops.
Curing Methods
Curing can be performed by any of the following approaches:
- Maintaining the presence of water in the concrete during early ages: Methods to maintain the water pressure include ponding or immersion, spraying or fogging, and wet coverings.
- Preventing loss of mixing water from the concrete by sealing the surface: Methods to prevent water loss include impervious papers or plastic sheets, membrane-forming compounds, and leaving the forms in place.
- Accelerating the strength gain by supplying heat and additional moisture to the concrete: Accelerated curing methods include steam curing, insulating blankets or covers, and various heating techniques.
1. Ponding and immersion
On flat surfaces, such as pavements and floors, concrete can be cured by ponding. Ponding involves covering the exposed surface of the concrete structure with water. Ponding can be achieved by forming earth dikes around the concrete surface to retain water. Ponding is an ideal method for preventing loss of moisture from the concrete; it is also effective for maintaining a uniform temperature in the concrete. The curing water should not be more than about 11°C (20°F) cooler than the concrete to prevent thermal stresses that could result in cracking. Since ponding requires considerable labor and supervision, the method is generally used only for small jobs.
The most thorough method of curing with water consists of total immersion of the finished concrete element. This method is commonly used in the laboratory for curing concrete test specimens. Where appearance of the concrete is important, the water used for curing by ponding or immersion must be free of substances that will stain or discolor the concrete. The material used for dikes may also discolor the concrete.
2. Fogging and Spraying
Fogging and sprinkling with water are excellent methods of curing when the ambient temperature is well above freezing and the humidity is low. A fine fog mist is frequently applied through a system of nozzles or sprayers to raise the relative humidity of the air over flatwork, thus slowing evaporation from the surface. Fogging is applied to minimize plastic shrinkage cracking until finishing operations are complete. Once the concrete has set sufficiently to prevent water erosion, ordinary lawn sprinklers are effective if good coverage is provided and water runoff is of no concern. This method requires a large amount of water and could be expensive.
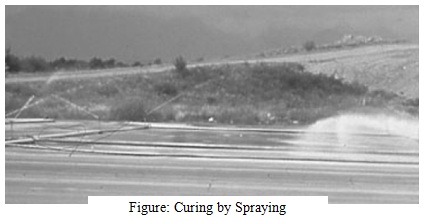
3. Wet Coverings
Fabric coverings saturated with water, such as burlap, cotton mats, rugs, or other moisture-retaining fabrics are commonly used for curing. The fabric can be kept wet, either by periodic watering or covering the fabric with polyethylene film to retain moisture. On small jobs, wet coverings of earth, sand, saw dust, hay, or straw can be used. Stains or discoloring of concrete could occur with some types of wet coverings.
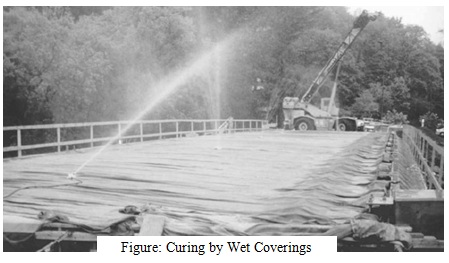
4. Impervious Papers
Impervious paper for curing concrete consists of two sheets of haft paper cemented together by a bituminous adhesive with fiber reinforcement. Such paper, conforming to ACTM C 171 (AASHTO M 171), is an efficient means of curing horizontal surfaces and structural concrete of relatively simple shapes. An important advantage of this method is that periodic additions of water are not required. Curing with impervious paper enhances the hydration of cement by preventing loss of moisture from the concrete.
In addition to curing, impervious paper provides some protection to the concrete against damage from subsequent construction activity as well as protection from the direct sun. It should be light in color and non-staining to the concrete. Paper with a white upper surface is preferable for curing exterior concrete during hot weather.
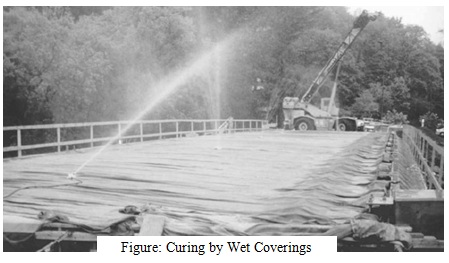
5. Membrane-Forming Curing Compounds
Liquid membrane-forming compounds consisting of waxes, resins, chlorinated rubber, and other materials can be used to retard or reduce evaporation of moisture from concrete. They are the most practical and most widely used method for curing not only freshly placed concrete but also for extending curing of concrete after removal of forms or after initial moist curing. However, the most effective methods of curing concrete are wet coverings or water spraying that keeps the concrete continually damp.
Curing compounds should be able to maintain the relative humidity of the concrete surface above 80% for seven days to sustain cement hydration. Curing compounds can be applied by hand or by using spray equipment. Either one coat or two coats (applied perpendicular to each other) are used. Normally, the concrete surface should be damp when the curing compound is applied.
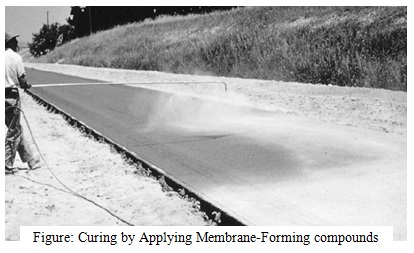
6. Steam Curing
Steam curing is advantageous where early strength gain in concrete is important or where additional heat is required to accomplish hydration, as in cold weather. Two methods of steam curing are used: live steam at atmospheric pressure (for enclosed cast-in-place structure and large precast concrete units) and high-pressure steam in autoclaves (for small manufactured units).
7. Forms left in Place
Forms provide satisfactory protection against loss of moisture if the top exposed concrete surfaces are kept wet. A soaker hose is excellent for this. The forms should be left on the concrete as long as practical.
Wood forms left in place should be kept moist by sprinkling, especially during hot, dry weather. If this cannot be done, they should be removed as soon as practical and another curing method started without delay. Color variations may occur from formwork and uneven water curing of walls.
8. Insulating Blankets or Covers
When the temperature falls below freezing (0°C), concrete should be insulated using layers of dry, porous material such as hay or straw. Formwork can be economically insulated with commercial blanket or batt insulation that has a tough moisture-proof covering. Suitable insulating blankets are manufactured of fiberglass, sponge rubber, cellulose fibers, mineral wool, vinyl foam, and open-cell polyurethane foam. When insulated formwork is used, care should be taken to ensure that concrete temperatures do not become excessive.
9. Electrical, Oil, Microwave, and Infrared Curing
Electrical, hot oil, microwave and infrared curing methods have been available for accelerated and normal curing of concrete for many years. Electrical curing includes electrically heated steel forms, and electrically heated blankets. Reinforcing steel can be used as a heating element, and concrete can be used as the electrical conductor. Steel forms can also be heated by circulating hot oil around the outside of the structure. Infrared rays have been used for concrete curing on a limited basis.
Curing Periods and Temperature
The curing period should be as long as is practical. The period of time that concrete should be protected from freezing, abnormally high temperatures, and against loss of moisture depends upon a number of factors: such as type of cement, mixture proportions, required strength, ambient weather, size and shape of the structure, future exposure conditions, and method of curing.
A higher curing temperature provides earlier strength gain in concrete than a lower temperature but it may reduce the 28-day strength. During cold weather, additional heat is often required to maintain favorable curing temperatures of l0oC to 20°C (50°F to 70°F).
Since the rate of hydration is influenced by cement type and the presence of supplementary cementing materials, the curing period should be prolonged for concretes made with cementing materials possessing slow-strength-gain characteristics. For mass concrete (large piers, locks, abutments, dams, heavy footings, and massive columns and transfer girders) in which no pozzolan is used as part of the cementitious material, curing of unreinforced sections should continue for at least 2 weeks. If the mass concrete contains a pozzolan, minimum curing time for unreinforced sections should be extended to 3 weeks. Heavily-reinforced mass concrete sections should be cured for a minimum of 7 days.
References
- Mamlouk, M.S. And Zaniewski J.P., Materials For Civil and Construction Engineers, 2011.